Nathan Grey from Sydney has never shied away from building a difficult shaped board and this is no exception. He has just got this new one finished.
"I had a go at at doing a Greenough style edge board.Vital statistics are. 6'1" 21" 2,5/8", It has got the single to double concave running the the central plane of the board, and I got myself a nice 8" hull flex fin from Alkali fins.
The Construction is hollow with rib's and no spine, the deck is paulownia and the rails and bottom skin are balsa. Glass job is 4oz top and bottom, entropy super sap epoxy."
Sunday, October 23, 2016
Sunday, October 16, 2016
Fish Fry Floripa Brasil
Last weekend sawthe first Fish Fry in Brasil that wasa organised by David Webber. He builds wooden boards and it looks like there were plenty of wooden boards there on the day
Felipe Siebert was there with some of his boards as well.
It looks like they had a great day
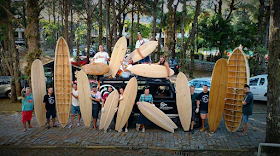
David Webber builds wooden boards and holds classes so if you need a board or want to build one contact him.
Thursday, October 13, 2016
Jon White and Knocker wooden surfboards
"I have attached photos of a 8.6’ Hybrid Fish, which is my latest build and my go to board for all UK conditions. The design mixes the characteristics and performance features of a thruster with the added width and tail design of a fish. I surf it as a quad, but it would work well as a twin. It has a more progressive rocker than the fish, a flat deck and like all my boards it has a hard rail shape.
The board is made from Paulownia timber that is now grown in Spain http://www.ipaulownia.co.uk. Having a good European supplier is a real plus for the UK and makes it affordable. Previously the only option was to import from China, Australia or the US.
The surfboards are designed on a CAD program before transferring the outline and profile to plywood templates. Each plank is then screwed on to the rocker template and cut on a bandsaw jig, much like you would make chair legs. This means that the rockers are 2mm thicker than I require, but exactly the required shape meaning that they only require an even sand for the final shape.
The individual rocker planks are then screwed together, with the middle two lightly glued to enable the outline and rails to be shaped. The board is then taken apart and chambered (thickness: 10mm top, 13mm or 10mm bottom, depending on the bottom shape). With out chambering, the boards weigh between 27 and 29 Kilos for a 100-litre board. Chambering a SUP brings this down by around 60%, as there is more area per volume of wood than would be the case for a traditional surfboard.
http://www.knockersurfboards.com.
The board is then glued together and given a final shape and sand down to 400 grit. Depending on the customer, I either added 7 coats of Le Tonkinois oil, or 3 coats over a ‘cheater coat’ of bio-epoxy resin. "
I have looked into this Le Tonkinois Oil as a finish and it is very interesting and a very old formula. But so far have not been able to find it here in Australia. Let me know if you find it anywhere.
http://www.letonkinoisvarnish.co.uk/varMain.html
The board is made from Paulownia timber that is now grown in Spain http://www.ipaulownia.co.uk. Having a good European supplier is a real plus for the UK and makes it affordable. Previously the only option was to import from China, Australia or the US.
The surfboards are designed on a CAD program before transferring the outline and profile to plywood templates. Each plank is then screwed on to the rocker template and cut on a bandsaw jig, much like you would make chair legs. This means that the rockers are 2mm thicker than I require, but exactly the required shape meaning that they only require an even sand for the final shape.
The individual rocker planks are then screwed together, with the middle two lightly glued to enable the outline and rails to be shaped. The board is then taken apart and chambered (thickness: 10mm top, 13mm or 10mm bottom, depending on the bottom shape). With out chambering, the boards weigh between 27 and 29 Kilos for a 100-litre board. Chambering a SUP brings this down by around 60%, as there is more area per volume of wood than would be the case for a traditional surfboard.
http://www.knockersurfboards.com.
The board is then glued together and given a final shape and sand down to 400 grit. Depending on the customer, I either added 7 coats of Le Tonkinois oil, or 3 coats over a ‘cheater coat’ of bio-epoxy resin. "
I have looked into this Le Tonkinois Oil as a finish and it is very interesting and a very old formula. But so far have not been able to find it here in Australia. Let me know if you find it anywhere.
http://www.letonkinoisvarnish.co.uk/varMain.html
Tuesday, October 11, 2016
Monday, October 3, 2016
It is time to experiment. It is always time to experiment.
I get lots of people emailing and asking questions about building wooden
boards and that is great. There are many ways of building wooden boards
and there are no right and wrong ways of doing it. Seeking advice is
great but in the end you need to get down to it and just do it.I find
that on forums there are more negative comments than helpful comments to
help people out.And some I would say come from people who have done
very little experimenting and it is all theory and hearsay.You are also
likely to come across people who know everything, which is interesting.
Sorry, just my experience.
One question I get asked alot about my use of lanolin on Paulownia and how it works.
I have built many boards with Paulownia and a lanolin finish. Paulownia grows very fast and straight so has a very long grain and if it gets a hit it will absorb the impact very well. If it dents you can use a stream iron and and a damp tea towel and it will swell out again. I have done it many times. If you look after your board you will find that it will look like new for a very long time.
The
Linseed oils and nut oils people use are vegetable and plant based oils that feel
slippery when applied ( which people find appealing ) and if you wash the board in fresh water then a grey mould can
grow in the soft grain of the wood. Where as Lanolin is an animal product and so it will not grow mould. It has a natural wax in it that
makes it waterproof and when it hits salt water you will not need to wax the board. If you soak plenty of it into the timber it will
seal and nourish the wood. Yes it is raw wood and like any furniture
it will need to be treated right and looked after.You are not making a
white foam surfboard as a piece of disposable sports equipment. Because your board is finished in raw wood with oil you will need to look after it. Don't wash it in fresh water ever. When you get it out of the surf , just wipe it down with a towel and let it air dry. Store it in a breathable cloth bag. Not a plastic / vinyl padded bag as it will stew in the heat if there is any moisture. Any raw timber will not fair well in these conditions. The moisture and heat will soften and break down the structure of the wood.
If you
are are building a hollow framed board you will need to be sure to have
good glue joints as the oil will not fill bad glue joints. Also the
skins will need to be thick enough and strong enough to do the job.You
may want to be safe the first time and seal the under side of the skins
with a coat of epoxy or varnish.
I use : lanotec.com.au they are a great local Australian company. I use their General Purpose Lanolin.
I have found that when using polyurethane glue and vacuum bagging skins onto EPS that as the glue foams and goes off it is forced in between the beads of the ESP. This depending on the grade of EPS can be up to 30mm deep. This in turn toughens the EPS and seals the structure under the wood.All positive things. I know this from cutting up boards to rout fin boxes in and cutting shapes into the tails and adding nose blocks.
With all these things you need to experiment and find a method you are happy with and a result you are happy with. It takes time and you may have failures but that is how you learn. That is the exciting part. You will learn a lot. If you change one component you can change the outcome. Human nature being what it is you will more than likely to overbuild your first attempt. We have all done that.You can think about it as much as you like , but at some stage you have to give it a go.
Let me know how you go.
One question I get asked alot about my use of lanolin on Paulownia and how it works.
I have built many boards with Paulownia and a lanolin finish. Paulownia grows very fast and straight so has a very long grain and if it gets a hit it will absorb the impact very well. If it dents you can use a stream iron and and a damp tea towel and it will swell out again. I have done it many times. If you look after your board you will find that it will look like new for a very long time.
![]() |
Just paint it on and leave it out in the sun to soak up. You will know when it won't take up any more. When it stops being sticky apply some more. No need for wax. |
![]() |
4 years old and surfed regularly in New Zealand. Still going strong in the UK now. |
I use : lanotec.com.au they are a great local Australian company. I use their General Purpose Lanolin.
I have found that when using polyurethane glue and vacuum bagging skins onto EPS that as the glue foams and goes off it is forced in between the beads of the ESP. This depending on the grade of EPS can be up to 30mm deep. This in turn toughens the EPS and seals the structure under the wood.All positive things. I know this from cutting up boards to rout fin boxes in and cutting shapes into the tails and adding nose blocks.
With all these things you need to experiment and find a method you are happy with and a result you are happy with. It takes time and you may have failures but that is how you learn. That is the exciting part. You will learn a lot. If you change one component you can change the outcome. Human nature being what it is you will more than likely to overbuild your first attempt. We have all done that.You can think about it as much as you like , but at some stage you have to give it a go.
Let me know how you go.
Mark Riley celebrates 20 years building Balsa Boards
Marks vision back in 1996 was to bring back the magic material of balsawood to relive the history and romance of the 1950's. Not only did Mark get swept away with the romance it was the physical properties of balsa with the strength to weight ratio that was extremely high which helped create boards that would last longer and never need to go to landfill. Every board is unique and hand built in Australia and stores carbon to help the environment.
Mark was recently fortunate to meet Ron Cansdell, who built about 150 balsa boards back in the 1950's.Mark had the pleasure of building and glassing a replica balsa board with Ron last month and also shared some great stories and photos with this icon of Australian surfing.
Mark would like to thank many people in helping him get to where he is today in this tough industry and he will do this with a celebration party at The New Sting Bar in Cronulla on the 13th October.
There will be pizza supplied, first release of his inaugural Papua New Guinea video including all info on the next trip to PNG to build a balsa board, all Aussie surf 80s rock beach music, lucky door prizes including a balsa board and Air Niugini tickets to PNG and many more prizes. Everyone is welcome to come down for a slice of pizza and action starting on Thursday 13th Oct at 6pm Sting Bar 3-7 Kingsway, Cronulla NSW 2230
http://www.balsawoodsurfboardsriley.com/
156 President Ave.,
Miranda 2228 NSW
Australia
Phone - 0412 376 464
Email - mark@riley.com.au
Facebook -https://www.facebook.com/rileybalsa99/
Mark was recently fortunate to meet Ron Cansdell, who built about 150 balsa boards back in the 1950's.Mark had the pleasure of building and glassing a replica balsa board with Ron last month and also shared some great stories and photos with this icon of Australian surfing.
Mark would like to thank many people in helping him get to where he is today in this tough industry and he will do this with a celebration party at The New Sting Bar in Cronulla on the 13th October.
There will be pizza supplied, first release of his inaugural Papua New Guinea video including all info on the next trip to PNG to build a balsa board, all Aussie surf 80s rock beach music, lucky door prizes including a balsa board and Air Niugini tickets to PNG and many more prizes. Everyone is welcome to come down for a slice of pizza and action starting on Thursday 13th Oct at 6pm Sting Bar 3-7 Kingsway, Cronulla NSW 2230
A great effort Mark and we look forward to the next 20 years.
Riley Classic Balsawood Surfboardshttp://www.balsawoodsurfboardsriley.com/
156 President Ave.,
Miranda 2228 NSW
Australia
Phone - 0412 376 464
Email - mark@riley.com.au
Facebook -https://www.facebook.com/rileybalsa99/